An aviation engineer by profession, Kenneth Caruana takes a logical approach to all of life’s challenges. In fact, he often sees opportunities where the rest of us might see just problems. “Possibly it is my aviation background that allows me to think in a certain way,” Kenneth explains. “It is an attitude more than anything, that has inspired me to grow in this sector over the years.”
In fact, Kenneth is the man behind Thermoplastics Ltd, a local company which specialises in the production of injection moulded plastic items. “The versatility of our product is endless, and the possibilities infinite. We produce anything from toys to packaging, components for the automotive industry, custom carbon fibre products, engineered plastics as well as printing on plastic.”
Employing no less than 370 workers across two factories in Malta and Tunisia, and set to grow further, Thermoplastics Ltd serves a vast market in several economic sectors, around the world. “We are looking at an imminent expansion in our Tunisia plant which will grow to employ 500 employees.”
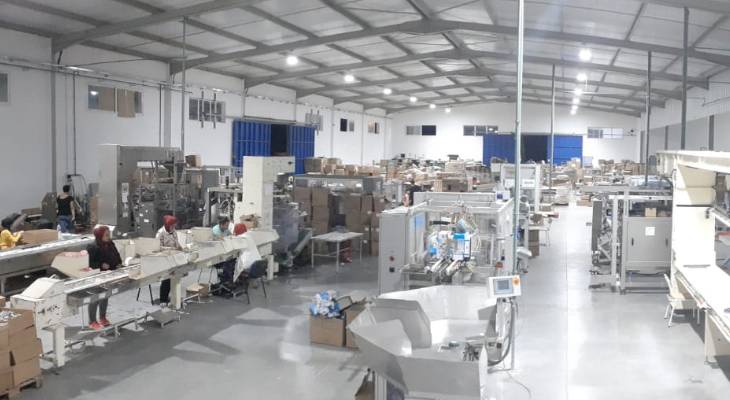
Thermoplastics Malta, along with one of its sister Companies, 2KR Designs, is in for some exciting plans, as it embarks on an ambitious and innovative project. “We are all familiar with the local beverage container deposit machines, a central element in Malta’s recycling efforts. With the local scheme, in fact, Malta was one of the first countries in the EU to put such an operation in action. By 2029, all other member states will be required to have a similar system in place. In this context, we are currently developing a smaller version of the reverse-vending machine (RVM), which will be produced more cheaply and will take up less space, which is great news for the smaller retailer,” Kenneth claims.
“We have researched the concept of an improved RVM thoroughly, and found a great opportunity for shops that cannot afford to invest in a large-scale one due to the prohibitive price point, and logistics. We are looking at the European market to propose our machines, as we will be increasing some 30 workers on our Maltese floor to meet the expected elevated demand,” Kenneth expounds.
With plastic increasingly becoming the centre of a debate of an environmental nature, Kenneth is very open about the effect the miracle material may have on the natural world.
“Plastic itself is not the problem, rather its irresponsible disposal is,” Kenneth clarifies right away. “It is a good thing that single-use plastics are being phased out. We stopped producing cheap single-use articles a long time ago, as they tend to be most likely to be irresponsibly disposed of. However, when used responsibly, plastic has improved our lives immeasurably,” Kenneth is keen to note.
In fact, from its humble origins in the 19th century, and over the decades, plastic has revolutionised the world of manufacturing, rendering the production of virtually most objects cheaper, faster, lighter and readily at the reach of almost anyone.
“A study we carried out, as a point of interest revealed that the cost of your average commercial car which retails at €40,000, would shoot up in price to around €110,000 if all the plastic elements were left out of the production line,” he explains.
If anything, plastic is too successful a material, in the sense that it is very hard to destroy or deteriorate in natural ways. However, industry has long been working on an alternative which would provide the same strength and advantages of the material, while being friendlier to the environment.
“First of all, our emphasis remains on sustainability and the responsible use of the materials we operate in. For instance, our entire operation is entirely waste zero, as all the off-cuts and waste-product generated when moulding our articles is once again recycled into fresh plastic that is used in the next run. This is a process that can take place an infinite number of times, hence no material ever goes to waste,” Kenneth notes.
“Clients can also opt to choose having their products entirely made from recycled plastics. We often offer this option to our clients, working closely with our team of experienced product designers, to provide the client with the best results according to their budget.”
“Furthermore, we are also using a new plastic that is changing the game completely, as it is derived completely from corn, making it completely biodegradable. Its characteristics remain akin to those of regular plastic, including weight and strength, however it is friendlier to the environment as it decomposes completely over time,” Kenneth explains.
Thermoplastics’ green credentials are more than evident, even in the daily running of the enterprise, as the whole organisation is pluri-certified under various ISO standards. “Often ISO certification is taken as a box-ticking burden – we like to think of it differently as we see in it an opportunity to improve our operation, increase sustainability and efficiency.”
Widening the scope of the conversation onto the manufacturing industry in general, Kenneth is confident about its permanence locally, as it provides a desired stability while contributing handsomely to the country’s national GDP.
“Manufacturing has come a long way from the Dickensian shop floors of old,” Kenneth quips. “What we used to refer to as factories, nowadays employ entire armies of highly motivated, and specialised professionals in environments that are practically laboratories rather than what you would imagine a factory to look like. Careers in manufacturing are as diverse as they are bountiful, with opportunities for specialisation and growth in practically any field. My advice to the younger generation is to seriously consider a career in manufacturing, as the satisfaction derived from being part of the creation process of something, is beyond words,” Kenneth concludes.
Main Image: